Les défis de la fabrication de dispositifs médicaux
Medtronic, l'un des principaux fabricants de dispositifs médicaux, dessert plus de 78 millions de personnes et traite plus de 70 problèmes de santé. Avec 95 000 employés répartis sur 350 sites dans le monde, l'échelle de ses opérations est immense. Toutefois, cette échelle entraîne également plusieurs défis :
Des processus manuels et basés sur le papier : Traditionnellement, la collecte de données sur les différents sites de production impliquait une saisie manuelle dans des feuilles de calcul et des presse-papiers. Cette méthode était sujette aux erreurs humaines, lente et inefficace.
Visibilité limitée et silos de données : les données de production étaient dispersées dans des systèmes déconnectés, ce qui empêchait une visibilité opérationnelle complète et en temps réel, ainsi qu'une optimisation globale.
Taux de rebut élevés : Les défauts de qualité étaient souvent identifiés trop tard dans le processus de production, ce qui entraînait un gaspillage de matériaux et de ressources.
Maintenance réactive : L'incapacité à identifier de manière proactive les problèmes liés aux équipements a entraîné des temps d'arrêt élevés et une dépendance à l'égard des données historiques pour les décisions de maintenance.
Gestion inefficace de la production : La difficulté à gérer les charges de travail et les lignes de production a affecté le débit et la qualité des produits, les goulets d'étranglement passant souvent inaperçus.
La solution : Perspectives IoT en temps réel
Pour relever ces défis, Medtronic s'est associé à Improving et à Confluent pour mettre en œuvre une solution basée sur des informations IoT en temps réel. L'approche repose sur trois piliers :
Capturer les données en temps réel : Les données ont été capturées directement à partir d'appareils, de capteurs et de systèmes IoT dans l'usine, y compris les systèmes d'exécution de la fabrication (MES) et les courtiers MQTT.
Mise en œuvre de pipelines de données en temps réel : Les données capturées ont été diffusées en continu dans Kafka, ce qui a permis de créer des rapports automatisés, des analyses et des applications en temps réel. Les applications Kafka Streams ont intégré la logique d'entreprise dans ces flux en temps réel.
Évolutivité et standardisation : L'utilisation de Confluent Cloud a permis de garantir une évolutivité fiable au fur et à mesure de l'ajout de nouveaux sites de production. La standardisation au sein de l'entreprise était cruciale pour une agrégation efficace des données.
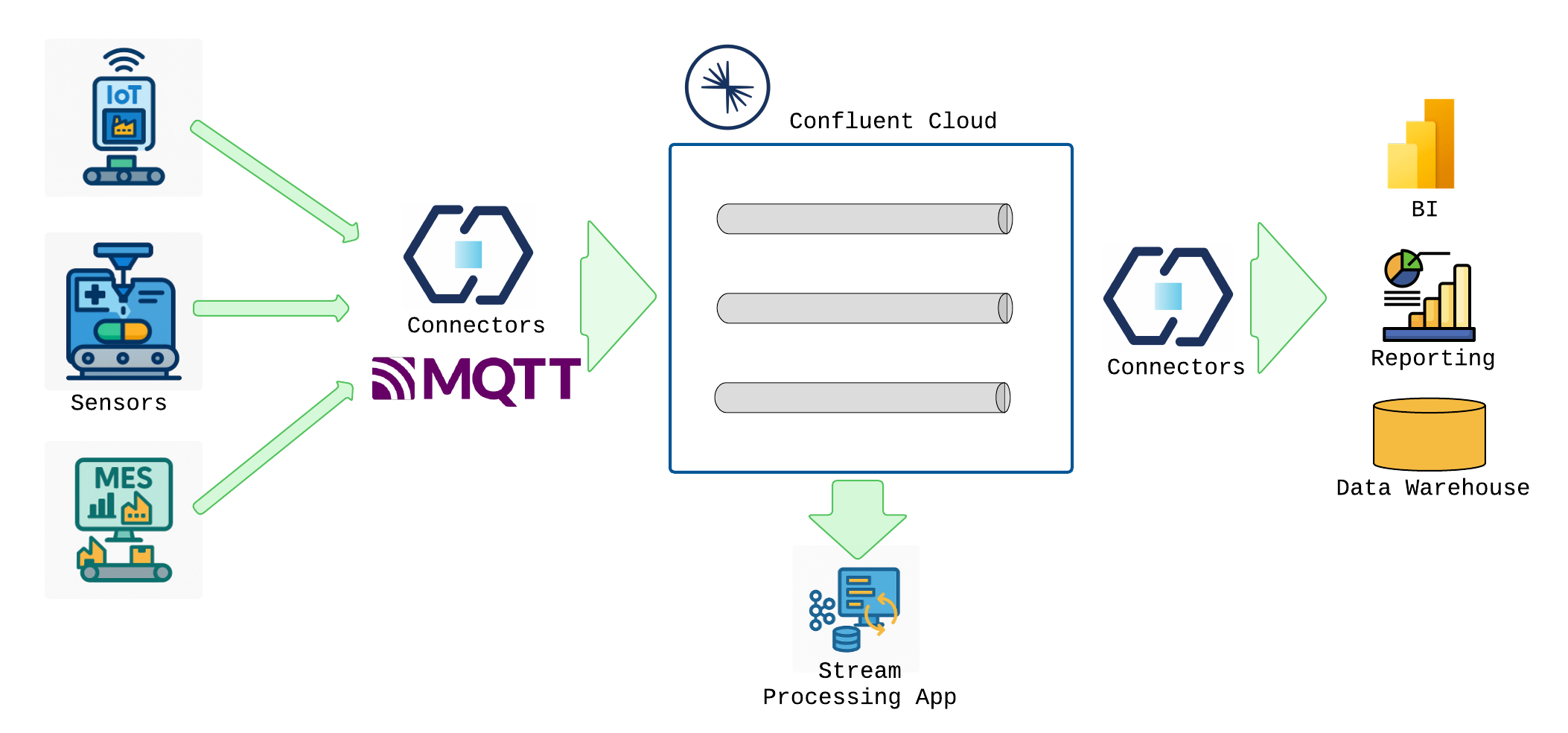
L'architecture technique
L'architecture de la solution fait appel à plusieurs technologies clés :
Appareils et capteurs IoT : Les données provenant des lignes de production ont été ingérées à l'aide des connecteurs Kafka Connect et MQTT.
Kafka et Confluent Cloud : Des flux de données ont été créés pour différents domaines et objectifs, transformant et enrichissant les données selon les besoins.
Power BI et entrepôts de données : Les systèmes en aval pour l'analyse et le reporting ont utilisé les données traitées.
Flux Kafka : Des applications en temps réel ont été créées pour exploiter directement les informations.
Cette architecture a transformé les processus manuels et par lots en processus automatisés et en temps réel, permettant aux applications et aux systèmes de reporting d'agir sur les données au fur et à mesure.
Avantages des informations IoT en temps réel
La mise en œuvre d'informations IoT en temps réel a apporté plusieurs avantages à Medtronic :
Improving Data Visibility (visibilité améliorée des données) : La visualisation des données en temps réel a permis une prise de décision plus rapide et de meilleure qualité.
Amélioration de l'efficacité opérationnelle : La collecte automatisée des données a rationalisé les processus, réduisant le besoin de saisie manuelle et augmentant la vitesse.
Réduction des coûts : La réduction des temps d'arrêt des équipements et l'optimisation des lignes de production ont permis de réaliser d'importantes économies.
Optimisation de la production : La visibilité en temps réel a permis d'identifier et de résoudre les goulets d'étranglement, améliorant ainsi l'efficacité de la production.
Maintenance proactive : L'analyse en temps réel a permis une maintenance prédictive, réduisant les temps d'arrêt et les coûts.
Évolutivité : L'architecture s'est adaptée efficacement à l'ajout de nouveaux sites, sans perte de performance ni remaniement important.
Enseignements tirés
L'aventure de la transformation n'a pas été sans difficultés. Les principaux enseignements tirés sont les suivants :
Patience dans la transformation : L'introduction progressive des pratiques numériques a permis une adoption et une intégration harmonieuses avec les capacités et la culture existantes.
Conception en fonction de l'échelle : La planification de l'évolutivité dès le départ a permis d'éviter la dégradation des performances au fur et à mesure de l'ajout de nouveaux sites.
Normalisation : L'établissement de modèles de données, de conventions de dénomination et de pratiques d'intégration standardisés a été crucial pour une agrégation efficace des données.
Utilisation efficace des partenariats : L'exploitation des capacités de partenaires tels que Confluent a été essentielle à la réussite du projet.
Capacité prédictive : Les données en temps réel ont permis une maintenance prédictive, réduisant de manière significative les temps d'arrêt et augmentant l'efficacité opérationnelle.
L'impact
La transformation des lignes de production de Medtronic grâce à des informations IoT en temps réel a eu un impact profond sur leur capacité à optimiser la production de dispositifs médicaux qui changent la vie et sauvent des vies. En s'appuyant sur des technologies avancées et les meilleures pratiques, Medtronic a amélioré son efficacité, réduit ses coûts et renforcé la qualité de ses produits. Ce parcours est un exemple précieux pour les autres fabricants qui cherchent à exploiter la valeur des données en temps réel dans leurs opérations.
Pour en savoir plus sur la façon dont Improving peut vous aider à transformer vos lignes de production grâce à des informations IoT en temps réel, contactez-nous dès aujourd'hui !