Los retos de la fabricación de dispositivos médicos
Medtronic, fabricante líder de dispositivos médicos, atiende a más de 78 millones de personas y trata más de 70 enfermedades. Con 95.000 empleados repartidos en 350 centros en todo el mundo, la escala de sus operaciones es inmensa. Sin embargo, esta escala también conlleva varios retos:
Procesos manuales y basados en papel: Tradicionalmente, la recogida de datos en los distintos centros de fabricación se realizaba manualmente en hojas de cálculo y portapapeles. Este método era propenso al error humano, lento e ineficiente.
Visibilidad limitada y silos de datos: los datos de producción estaban dispersos en sistemas desconectados, lo que impedía una visibilidad operativa completa y en tiempo real y una optimización global.
Elevadas tasas de rechazo: Los defectos de calidad se identificaban a menudo demasiado tarde en el proceso de producción, lo que suponía un desperdicio de materiales y recursos.
Mantenimiento reactivo: La incapacidad de identificar proactivamente los problemas de los equipos provocaba un elevado tiempo de inactividad y una dependencia de los datos históricos para tomar decisiones de mantenimiento.
Gestión ineficaz de la producción: La dificultad para gestionar las cargas de trabajo y las líneas de producción afectaba al rendimiento y a la calidad del producto, ya que los cuellos de botella a menudo pasaban desapercibidos.
La solución: Información de IoT en tiempo real
Para hacer frente a estos retos, Medtronic se asoció con Improving y Confluent para implementar una solución basada en información de IoT en tiempo real. El enfoque constaba de tres pilares:
Captura de datos en tiempo real: Los datos se capturaron directamente de los dispositivos, sensores y sistemas IoT de la planta de producción, incluidos los sistemas de ejecución de fabricación (MES) y los intermediarios MQTT.
Implementación de canalizaciones de datos en tiempo real: Los datos capturados se transmitieron a Kafka, lo que permitió la generación automatizada de informes, análisis y aplicaciones en tiempo real. Las aplicaciones Kafka Streams integraron la lógica empresarial en estos flujos en tiempo real.
Escalabilidad y estandarización: Construir sobre Confluent Cloud garantizó una escalabilidad fiable a medida que se añadían nuevas ubicaciones de fabricación. La estandarización en toda la empresa era crucial para una agregación de datos eficiente.
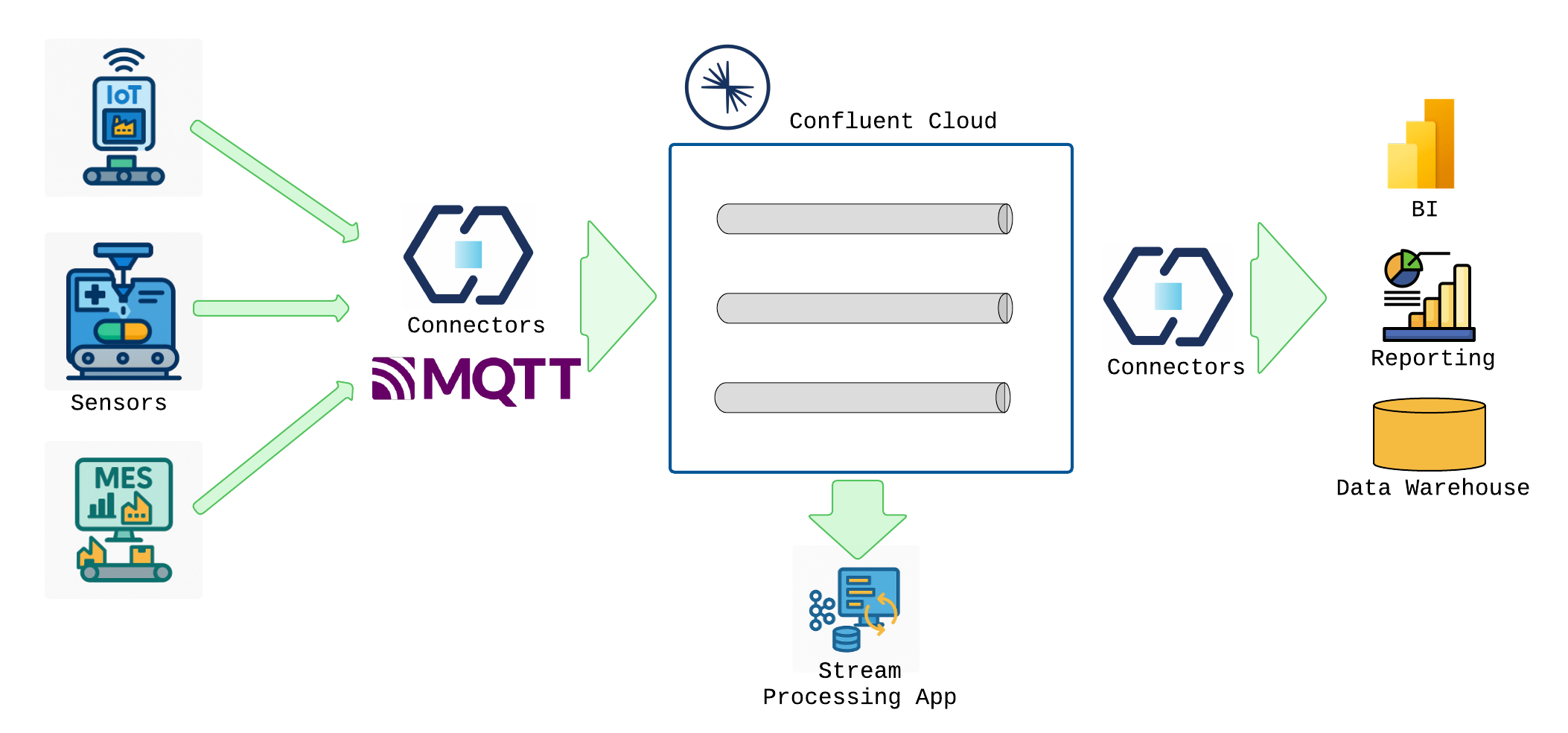
La arquitectura técnica
La arquitectura de la solución incluía varias tecnologías clave:
Dispositivos IoT y sensores: Los datos de las líneas de producción se ingestaron mediante conectores Kafka Connect y MQTT.
Kafka y Confluent Cloud: Se crearon flujos de datos para diferentes dominios y propósitos, transformando y enriqueciendo los datos según fuera necesario.
Power BI y almacenes de datos: Los sistemas descendentes para análisis e informes utilizaron los datos procesados.
Kafka Streams: Se crearon aplicaciones en tiempo real para actuar directamente sobre la información.
Esta arquitectura transformó los procesos manuales por lotes en procesos automatizados en tiempo real, permitiendo que las aplicaciones y los sistemas de generación de informes actuaran sobre los datos a medida que se producían.
Ventajas de la información de IoT en tiempo real
La implementación de información de IoT en tiempo real aportó varias ventajas a Medtronic:
Improving Data Visibility: La visualización de datos en tiempo real permitió una toma de decisiones más rápida y mejor.
Mayor eficiencia operativa: La recopilación automatizada de datos agilizó los procesos, reduciendo la necesidad de entrada manual y aumentando la velocidad.
Ahorro de costes: La reducción del tiempo de inactividad de los equipos y la optimización de las líneas de producción supusieron un importante ahorro de costes.
Rendimiento de producción optimizado: La visibilidad en tiempo real ayudó a identificar y resolver los cuellos de botella, Improving production efficiency.
Mantenimiento proactivo: Los análisis en tiempo real permitieron un mantenimiento predictivo, reduciendo el tiempo de inactividad y los costes.
Escalabilidad: La arquitectura se amplió eficientemente a medida que se añadían nuevos centros, sin pérdida de rendimiento ni grandes modificaciones.
Lecciones aprendidas
El proceso de transformación no estuvo exento de dificultades. Entre las principales lecciones aprendidas figuran las siguientes
Paciencia en la transformación: La introducción gradual de prácticas digitales garantizó una adopción sin problemas y la integración con las capacidades y la cultura existentes.
Diseño a escala: La planificación de la escalabilidad desde el principio evitó la degradación del rendimiento a medida que se añadían nuevas sedes.
Normalización: El establecimiento de modelos de datos estándar, convenciones de nomenclatura y prácticas de integración fue crucial para la agregación eficiente de datos.
Uso eficaz de las asociaciones: Aprovechar las capacidades de socios como Confluent fue esencial para el éxito.
Capacidad predictiva: Los datos en tiempo real permitieron el mantenimiento predictivo, reduciendo significativamente el tiempo de inactividad e impulsando la eficiencia operativa.
El impacto
La transformación de las líneas de producción de Medtronic a través de los conocimientos de IoT en tiempo real ha tenido un profundo impacto en su capacidad para optimizar la producción de dispositivos médicos que cambian y salvan vidas. Al aprovechar las tecnologías avanzadas y las mejores prácticas, Medtronic ha mejorado la eficiencia, reducido los costes y mejorado la calidad de sus productos. Este viaje sirve de valioso ejemplo para otros fabricantes que buscan liberar el valor de los datos en tiempo real en sus operaciones.
Para obtener más información sobre cómo Improving puede ayudar a transformar sus líneas de producción con información de IoT en tiempo real, póngase en contacto con nosotros hoy mismo.